On the market, there is a considerable demand for bleached panels or panels with a surface as uniform as possible. The irregular veins of wood can cause problems in the case of subsequent painting or with the veneering of very thin slices. This is why bleaching systems can greatly reduce the dark veins of wood, making the surface very uniform in color. This process is widely used by poplar plywood manufacturers but can also be used on okoume plywood or birch plywood.
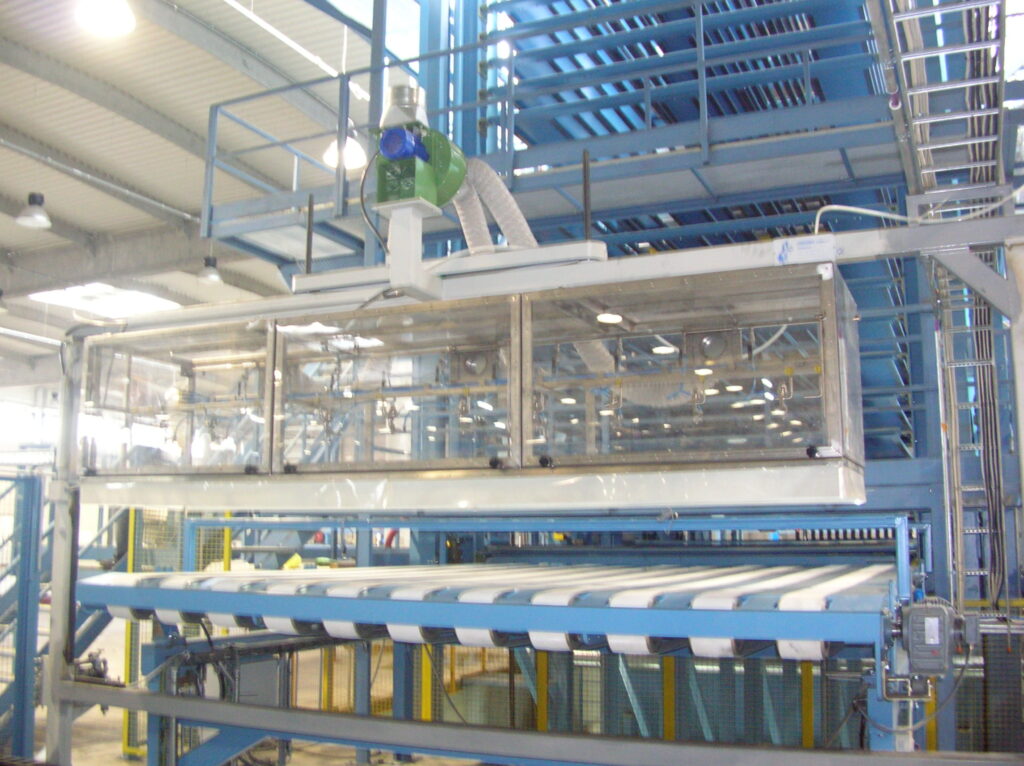
Introducing the plywood bleaching system, specifically designed hoods equipped with a battery of airbrushes suitable for nebulizing Hydrogen Peroxide, also known as oxygenated water, usually at 130 Vol. The oxygenated water is available in the market as an aqueous solution, and its concentration is indicated by the so-called “volumes”, which refer to the number of liters of oxygen that can be developed in normal conditions from one liter of aqueous solution of H2O2. For example, one liter of H2O2 solution at 5 volumes can develop 5 liters of oxygen and corresponds to a concentration of 1.46% by weight.
Bleaching systems function by nebulizing Hydrogen Peroxide onto wood panels or veneers just before they enter the hot press. The chemicals then evaporate, leaving no trace on the wood surface.
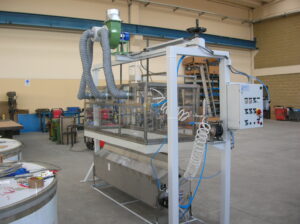
The bleaching systems can work on both sides, or just one of two sides and can have different width up to 2600mm. The system for whitening the upper side of the panel are made with a stainless steel structure and a transparent polycarbonate coating, while the systems for whitening the lower side of the panel are entirely made of stainless steel. The airbrushes are also made of stainless steel.
The line is composed of several other components, including a support structure for the aspirator, a stainless steel basket filter, a pneumatic pump in stainless steel, and a control panel.
The cylindrical stainless steel basket filter is used for filtering hydrogen peroxide before it reaches the airbrushes, and it comes with a special filtering sock. The filtering socks can have different filtering degrees according to the customer’s needs. The dimensions and filtering capacity of the basket filters can also vary based on the size of the system and the amount of product to be treated. The filter must be cleaned regularly based on its usage.
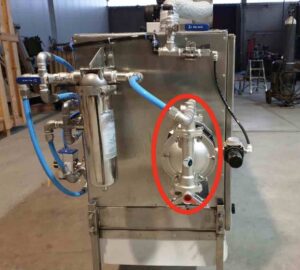
Each system comes equipped with a pneumatic pump with a stainless steel body. The pump has a suction collector and a discharge collector connected to the filter. It is recommended to position the storage tank of the Hydrogen Peroxide at a higher level than the pump so that the suction collector of the pump is lower than the suction collector positioned on the tank. It is also advisable to use a suction tube with a diameter equal to or greater than the suction collector’s diameter of the pump.
The control panel is equipped with a PLC to manage the machine’s functions in automatic cycle. The system can work in manual or automatic cycle, selectable from the appropriate selector on the control panel.
In manual mode, the start and stop of the spray are manually controlled by the operator using an ON/OFF selector. In automatic mode, the system starts and stops the spray automatically by means of a photocell positioned on the upper hood’s edge. The intervention times of the photocell can be adjusted from the operator panel on the control panel.
If you are looking for a reliable supplier of this product or you need more technical information, please contact me using the form on this page.
If you want to improve the information I provided on this page, or you simply want to add your comments or experience about this product, feel free to post a comment below.